Field Service Management with Built-In Maintenance Manual Access
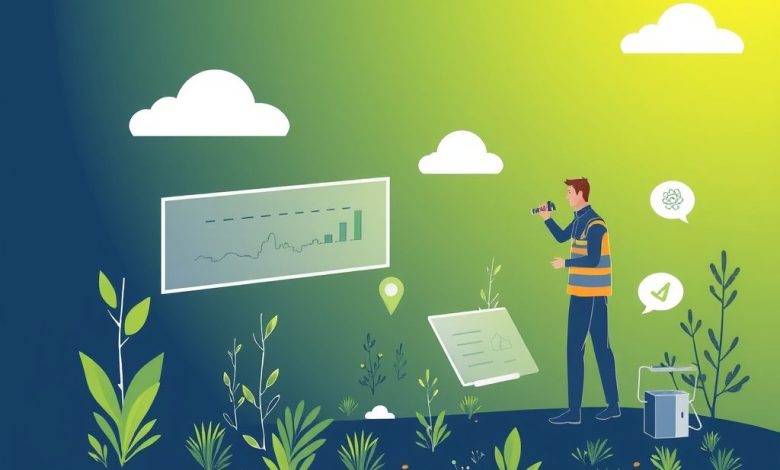
Introduction
Field Service Management (FSM) software has become increasingly crucial for businesses operating in various industries, particularly those involved in maintenance and repair services. As technology continues to advance, FSM solutions have evolved to incorporate more features and functionalities, enhancing efficiency and productivity for field service professionals. One such feature that has gained significant attention is the built-in maintenance manual access within FSM platforms.
The Importance of Field Service Management
Field Service Management software is designed to streamline operations for companies that send technicians or representatives to customers’ locations to perform maintenance, repairs, or installations. These platforms typically offer a range of features including:
- Scheduling and dispatching
- Resource allocation
- Inventory management
- Customer relationship management
- Reporting and analytics
By implementing FSM software, businesses can improve their operational efficiency, reduce costs, and enhance customer satisfaction.
The Role of Maintenance Manuals in Field Service Management
Maintenance manuals play a crucial role in ensuring that field technicians have access to accurate and up-to-date information about the equipment they are working on. Traditionally, these manuals were physical documents stored in warehouses or provided as paper copies to technicians. However, with the advent of digital technologies, many FSM platforms now incorporate built-in maintenance manual access.
This feature allows technicians to quickly reference repair procedures, troubleshooting steps, and safety guidelines directly from their mobile devices while on-site. This instant access to information can significantly reduce the time spent searching for solutions and minimize errors caused by outdated or incorrect information.
Benefits of Built-In Maintenance Manual Access
The inclusion of built-in maintenance manuals within FSM platforms offers several advantages for field service operations:
- Improved Efficiency: Technicians can quickly access the information they need without having to search through physical documents or navigate multiple websites.
- Consistency: Ensures all technicians have access to the same up-to-date information, reducing errors caused by outdated procedures.
- Cost Savings: Eliminates the need for paper manuals and reduces the cost associated with maintaining and distributing physical documentation.
- Enhanced Customer Satisfaction: Faster resolution of issues leads to improved customer satisfaction and loyalty.
- Reduced Training Time: New technicians can quickly familiarize themselves with equipment and procedures using the built-in manual feature.
Implementation and Integration
Implementing a FSM platform with built-in maintenance manual access typically involves the following steps:
- Choose a suitable FSM software that includes this feature.
- Upload digital versions of maintenance manuals to the platform.
- Organize manuals by equipment type or model for easy navigation.
- Ensure all technicians have access to the platform and understand how to use it effectively.
- Regularly update manuals to reflect any changes or updates to equipment specifications or repair procedures.
Challenges and Considerations
While the inclusion of built-in maintenance manual access is beneficial, there are some challenges to consider:
- Data Management: Ensuring that all necessary manuals are uploaded and kept up-to-date can be time-consuming and require significant effort.
- Compatibility Issues: Some older equipment may not have digital manuals available, requiring a mix of digital and physical resources.
- Security Concerns: Ensuring that sensitive information contained in manuals is properly secured and accessed only by authorized personnel.
- User Adoption: Some technicians may resist changing their traditional methods of accessing information, requiring training and support.
Case Study: XYZ Corporation
XYZ Corporation, a leading provider of HVAC services, implemented a FSM platform with built-in maintenance manual access. The company reported significant improvements in their operational efficiency:
- Technician response times decreased by 30%
- First-time fix rates increased by 25%
- Customer complaints about delayed resolutions dropped by 40%
These results were achieved primarily due to the instant access technicians had to accurate and up-to-date repair procedures and troubleshooting guides.
Conclusion
Field Service Management with built-in maintenance manual access represents a significant advancement in the industry. By providing technicians with quick and easy access to comprehensive repair information, businesses can improve their overall performance and customer satisfaction. As technology continues to evolve, we can expect even more sophisticated features to be integrated into FSM platforms, further enhancing the capabilities of field service professionals.
For companies looking to optimize their field service operations, incorporating a FSM solution with built-in maintenance manual access should be considered as part of their strategy to stay competitive in today’s fast-paced business environment.