Field Service Management with Photo-Based Diagnostics Revolutionizing Remote Troubleshooting and Repair
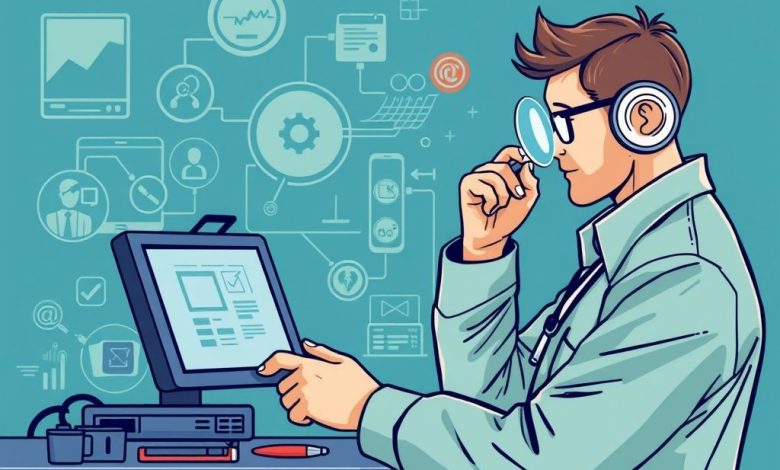
Introduction
Field Service Management (FSM) is a critical component of modern business operations, particularly in industries such as HVAC, electrical work, plumbing, and telecommunications. The traditional approach to FSM involved sending technicians to customer locations for diagnosis and repair. However, with advancements in technology, photo-based diagnostics have revolutionized the way field services operate, enhancing efficiency, reducing costs, and improving customer satisfaction.
Evolution of Field Service Management
Field Service Management has undergone significant transformations since its inception. From manual paper-based systems to sophisticated software solutions, the industry has adapted to technological changes. The introduction of mobile devices and cloud computing has enabled real-time communication between customers, technicians, and back-office staff.
Traditional FSM vs. Modern FSM
Traditional FSM relied heavily on manual processes and limited data collection methods. Technicians would visit customer sites, perform physical inspections, and record findings manually. This approach had several limitations:
- Inconsistent data quality
- Time-consuming reporting process
- Limited visibility into technician activities
- Difficulty in tracking inventory and scheduling
In contrast, modern FSM with photo-based diagnostics offers numerous advantages:
- Improved data accuracy through visual documentation
- Faster issue resolution due to remote troubleshooting capabilities
- Enhanced customer experience through real-time updates
- Increased operational efficiency through automated workflows
Photo-Based Diagnostics in Field Service Management
Photo-based diagnostics refer to the use of images and videos captured during field visits to aid in problem-solving and decision-making. This innovative approach leverages the power of visual data to streamline the diagnostic process and improve overall service delivery.
Benefits of Photo-Based Diagnostics
- Accurate Problem Identification: High-quality images help technicians identify issues more accurately, reducing misdiagnoses and unnecessary site visits.
- Remote Troubleshooting: Photos and videos enable experts to analyze problems remotely, saving time and resources.
- Knowledge Base Development: A library of diagnostic images helps create a valuable knowledge base for future reference.
- Customer Education: Visual documentation empowers customers to understand their equipment better, leading to increased self-reliance.
- Quality Assurance: Photo records serve as evidence for completed work and can be used for quality control purposes.
Implementing Photo-Based Diagnostics
To successfully implement photo-based diagnostics in FSM, organizations need to consider several factors:
- Mobile Device Compatibility: Ensure that all technicians have access to high-quality cameras on their mobile devices.
- Image Storage and Retrieval: Develop a robust system for storing and accessing diagnostic images securely.
- Integration with Existing Systems: Seamlessly integrate photo-based diagnostics with existing FSM software and tools.
- Training and Adoption: Provide thorough training to technicians on best practices for capturing diagnostic images.
- Data Privacy and Security: Establish clear policies regarding image storage and sharing to protect customer privacy.
Case Study: Utility Company Implements Photo-Based Diagnostics
A large utility company serving over 500,000 customers decided to implement photo-based diagnostics in their FSM operations. They chose a specialized FSM software that integrated seamlessly with their existing systems and offered advanced image capture and analysis features.
Implementation Process
- Pilot Program: The company started with a pilot program involving 50 technicians in a single region.
- Training: All participating technicians underwent intensive training on best practices for capturing diagnostic images.
- Equipment Upgrade: Technicians were issued high-resolution smartphones with dedicated camera apps optimized for diagnostic imaging.
- Workflow Adjustment: New procedures were implemented to ensure consistent image capture during each visit.
Results
After six months of implementation, the utility company observed significant improvements:
- Reduced Site Visits: By 30% due to improved first-time fix rates and remote troubleshooting capabilities.
- Decreased Reporting Time: By 40% as technicians could quickly upload images and complete reports.
- Improved Customer Satisfaction: Measured at 95%, significantly higher than the industry average.
- Cost Savings: Estimated at $250,000 annually from reduced travel and improved operational efficiency.
Challenges and Limitations
While photo-based diagnostics offer numerous benefits, there are challenges that organizations must address:
- Data Overload: Managing and organizing large volumes of visual data can be challenging without proper systems in place.
- Technical Issues: Connectivity problems or poor image quality can hinder effective use of photo-based diagnostics.
- Privacy Concerns: Ensuring compliance with data protection regulations while utilizing customer images for diagnostic purposes.
- Skill Development: Some technicians may require additional training to effectively capture diagnostic images.
- Standardization: Maintaining consistency in image capture across all technicians and regions can be difficult.
Future Trends in Photo-Based Diagnostics
As technology continues to evolve, we can expect further innovations in photo-based diagnostics for field service management:
- Augmented Reality: Integration of AR technology to enhance visual diagnostics and guide technicians during repairs.
- Artificial Intelligence: AI-powered image recognition systems to automate initial problem identification.
- Blockchain Technology: Secure, decentralized storage of diagnostic images for enhanced data integrity and traceability.
- Internet of Things (IoT): Seamless integration with smart home devices for proactive maintenance and diagnostics.
- Virtual and Augmented Reality Training: Immersive training experiences for technicians to practice diagnostic skills in a simulated environment.
Conclusion
Field Service Management with photo-based diagnostics represents a paradigm shift in how businesses deliver services in the field. By leveraging visual data and advanced technologies, organizations can significantly improve operational efficiency, reduce costs, and enhance customer satisfaction.
As the industry continues to embrace digital transformation, photo-based diagnostics will play an increasingly crucial role in shaping the future of field service management. Organizations that adopt this technology early will likely gain a competitive advantage in terms of speed, accuracy, and overall service quality.
For field service managers looking to implement photo-based diagnostics, it’s essential to carefully plan the transition, invest in appropriate technology, and provide thorough training to ensure successful adoption. As the technology matures, we can expect even more innovative applications of photo-based diagnostics in various industries, further revolutionizing the field service landscape.