Field Service Management for Smart Warehouse Equipment
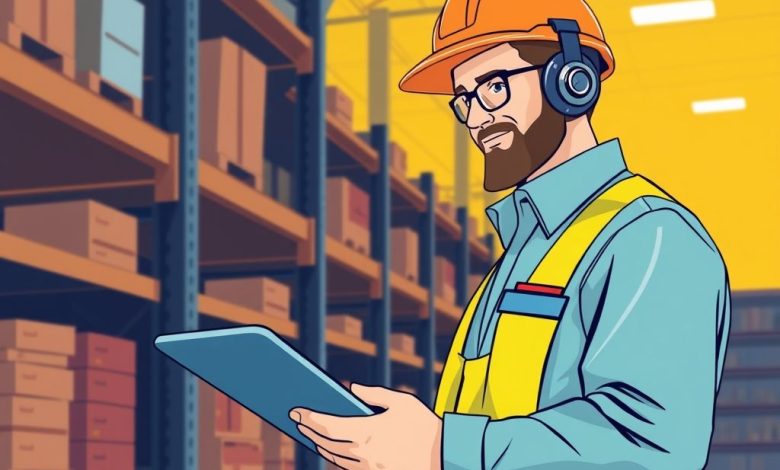
Field Service Management for Smart Warehouse Equipment
Introduction
In today’s rapidly evolving technological landscape, the integration of smart equipment in warehouses has revolutionized the way businesses operate. One crucial aspect of this transformation is Field Service Management (FSM) for smart warehouse equipment. This innovative approach combines cutting-edge technology with efficient management practices to streamline operations, enhance productivity, and improve overall efficiency.
The Rise of Smart Warehouse Equipment
Smart warehouse equipment refers to intelligent systems that utilize Internet of Things (IoT) technologies to monitor, control, and optimize various processes within a warehouse environment. These advanced tools can range from automated storage and retrieval systems to intelligent inventory management solutions.
The adoption of smart equipment has brought numerous benefits to warehousing operations:
- Improved accuracy in tracking and managing inventory
- Enhanced safety measures through real-time monitoring
- Increased efficiency in order fulfillment and shipping processes
- Reduced labor costs through automation
- Better decision-making based on data-driven insights
The Importance of Field Service Management
Field Service Management (FSM) is a critical component in maintaining the optimal performance of smart warehouse equipment. It encompasses all aspects of managing field technicians, scheduling service calls, and ensuring timely resolutions to equipment-related issues.
Effective FSM for smart warehouse equipment involves:
- Real-time monitoring of equipment status
- Predictive maintenance scheduling
- Efficient routing and dispatching of service technicians
- Centralized data management and reporting
By implementing robust FSM systems, businesses can significantly reduce downtime, improve customer satisfaction, and maintain a competitive edge in the market.
Key Components of Field Service Management for Smart Warehouse Equipment
#### IoT Integration
IoT technology plays a pivotal role in modern FSM systems for smart warehouse equipment. By integrating various devices and sensors throughout the warehouse, FSM software can gather real-time data on equipment performance, environmental conditions, and operational metrics.
This integration enables:
- Remote monitoring of equipment health
- Proactive identification of potential issues before they occur
- Automated alerts for maintenance requirements
- Optimization of resource allocation based on actual usage patterns
#### Real-time Monitoring
Real-time monitoring is a cornerstone of effective FSM for smart warehouse equipment. This feature allows field service managers to track equipment performance in real-time, enabling swift response to any issues that may arise.
Key benefits of real-time monitoring include:
- Immediate detection of equipment malfunctions
- Prioritization of service calls based on urgency
- Enhanced visibility into overall warehouse operations
- Improved decision-making through access to current data
#### Predictive Maintenance
Predictive maintenance is a game-changing aspect of FSM for smart warehouse equipment. By analyzing historical data and current equipment performance, FSM systems can predict when maintenance will be required, reducing unexpected breakdowns and associated downtime.
The advantages of predictive maintenance include:
- Scheduling maintenance at optimal times to minimize disruption
- Extending the lifespan of equipment through proactive care
- Reducing repair costs by addressing issues before they become critical
- Improving overall equipment reliability and efficiency
Implementing Effective Field Service Management
To ensure the success of FSM for smart warehouse equipment, organizations should consider the following best practices:
- Invest in comprehensive FSM software that integrates seamlessly with existing warehouse management systems.
- Provide thorough training to field technicians on the operation and maintenance of smart equipment.
- Establish clear communication channels between field technicians, warehouse staff, and management teams.
- Regularly review and update FSM processes to align with evolving technology and business needs.
- Foster a culture of continuous improvement within the field service team.
Challenges and Considerations
While FSM for smart warehouse equipment offers numerous benefits, organizations should be aware of potential challenges:
- Initial investment costs for implementing advanced FSM systems
- Ensuring adequate cybersecurity measures to protect sensitive data
- Managing the transition from traditional to modern FSM practices
- Addressing potential resistance to change among staff members
By proactively addressing these challenges, businesses can maximize the return on investment in FSM solutions for smart warehouse equipment.
Conclusion
Field Service Management for smart warehouse equipment represents a significant leap forward in optimizing warehousing operations. By leveraging IoT integration, real-time monitoring, and predictive maintenance capabilities, organizations can achieve unprecedented levels of efficiency, productivity, and customer satisfaction.
As technology continues to evolve, it is crucial for field service managers to stay abreast of emerging trends and best practices in FSM. By doing so, they can ensure that their organizations remain competitive in an increasingly digitalized and interconnected world.
The future of warehousing lies in the seamless integration of smart equipment and intelligent management systems. Field Service Management plays a vital role in realizing this vision, enabling businesses to harness the full potential of their smart warehouse investments and drive sustainable growth in the face of ever-increasing competition and market demands.